Why plastic extrusion is ideal for mass production
Wiki Article
Discovering the Numerous Strategies and Technologies Behind Plastic Extrusion
The world of plastic extrusion is a mix of innovation, precision, and technology, essential to many markets worldwide - plastic extrusion. Advanced machinery, computerized controls, and an array of products assemble in this complex procedure, generating high-grade, long lasting products. As the industry progresses, a shift towards lasting materials and intelligent equipment appears. The following conversation will certainly shed light on these strategies and innovations, while also meaning the interesting future prospects of this critical production procedure.Understanding the Fundamentals of Plastic Extrusion
The procedure of plastic extrusion, frequently hailed as a foundation in the realm of production, creates the bedrock of this discussion. Basically, plastic extrusion is a high-volume production procedure in which raw plastic product is melted and formed into a continual account. It's a method widely utilized for producing things with a constant cross-sectional account, such as pipes, window frameworks, and weather condition removing. The procedure begins with feeding plastic materials, typically in the kind of pellets, right into a warmed barrel. There, it is warmed and combined till it comes to be molten. The molten plastic is then required with a die, forming it right into the preferred type as it cools down and solidifies.The Role of Various Products in Plastic Extrusion
While plastic extrusion is a commonly used strategy in production, the products made use of in this procedure considerably influence its final output. Different kinds of plastics, such as polyethylene, PVC, and ABS, each lend unique residential properties to the end product. Polyethylene, known for its durability and adaptability, is often made use of in packaging, while PVC, renowned for its strength and resistance to ecological elements, is made use of in construction. ABS, on the various other hand, combines the most effective qualities of both, resulting in high-impact resistance and sturdiness. The option of material not just impacts the item's physical homes yet likewise affects the extrusion speed and temperature level. As a result, manufacturers need to thoroughly consider the properties of the material to maximize the extrusion process.Strategies Used in the Plastic Extrusion Process
The plastic extrusion procedure includes different methods that are critical to its procedure and efficiency (plastic extrusion). The discussion will start with a simplified explanation of the fundamentals of plastic extrusion. This will be complied with by a failure of the procedure carefully and an expedition of approaches to boost the performance of the extrusion strategy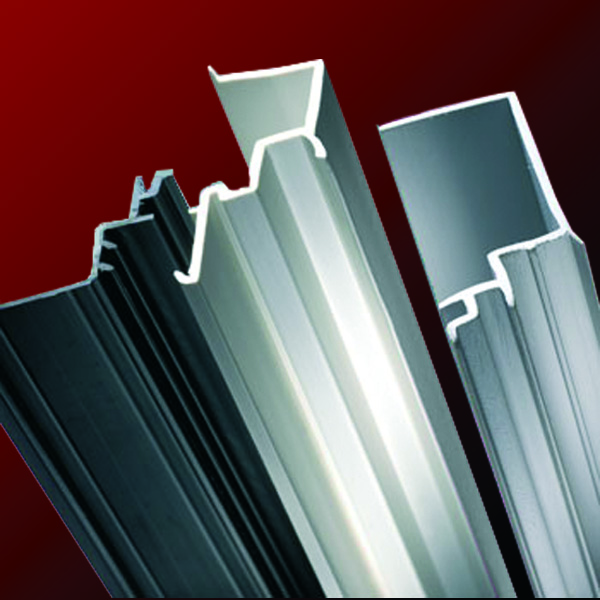
Recognizing Plastic Extrusion Basics
In the world of production, plastic extrusion stands as an essential process, essential in the manufacturing of a plethora of daily products. At its core, plastic extrusion includes changing raw plastic product into a continuous profiled form. This is accomplished by melting the plastic, often in the kind of granules or pellets, and forcing it via a designed die. The resulting product is a long plastic item, such as a panel, pipeline, or cable finish, that keeps the shape of the die. This cost-efficient technique is very flexible, able to create intricate forms and suit a wide range of plastic products. Fundamental understanding of these fundamentals allows for more exploration of the extra elaborate facets of plastic extrusion.Detailed Extrusion Process Breakdown
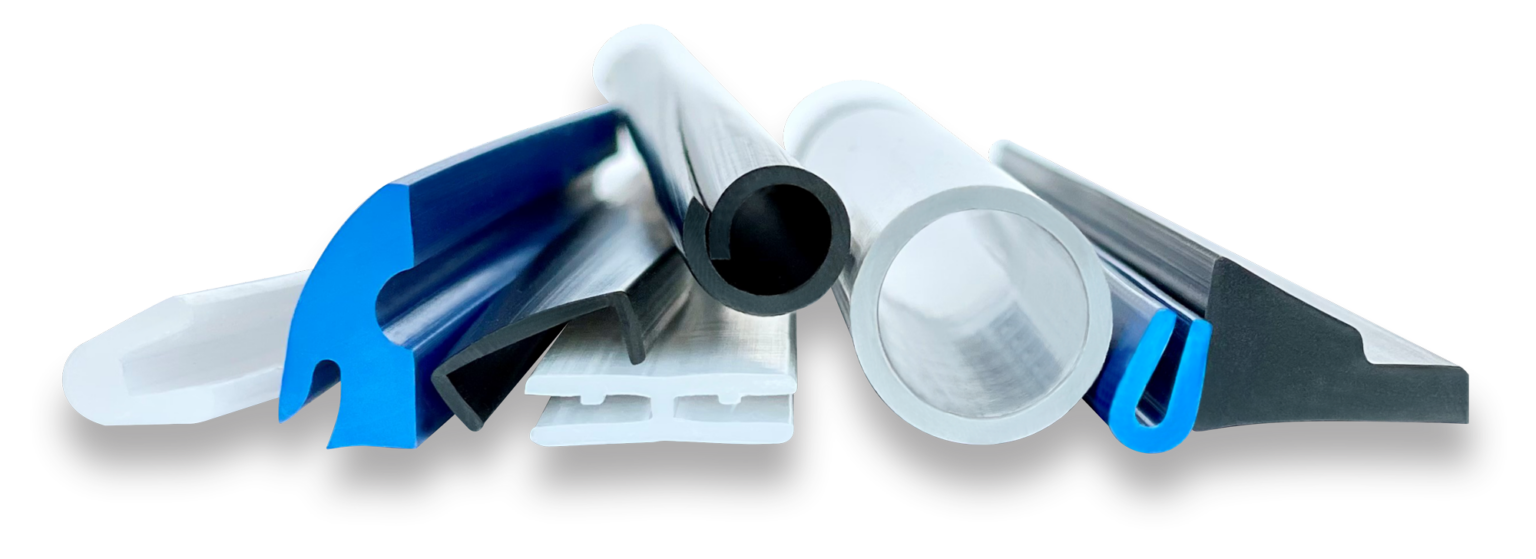
Improving Extrusion Strategy Performance
Effectiveness gains in the plastic extrusion procedure can significantly impact both the high quality of the last item and the overall productivity of the operation. Constant optimization of the extrusion method is essential to maintaining a competitive edge. Routine maintenance of extrusion devices can likewise lessen downtimes, hence increasing productivity.How Innovation Is Altering the Face of Plastic Extrusion
The development of new innovation has actually dramatically changed the landscape of plastic extrusion. It has actually caused the growth of sophisticated extrusion equipment, which has improved the efficiency and quality of the plastic extrusion process. Innovations in the extrusion process have actually additionally been driven by technical developments, providing improved capacities and adaptability.Advanced Extrusion Machinery
Changing the realm of plastic extrusion, advanced equipment imbued with sophisticated technology is ushering in a brand-new era of efficiency and precision. These machines, geared up with ingenious attributes like self-regulating temperature level control systems, make certain optimal conditions for plastic processing, consequently reducing waste and boosting item quality. While these developments are already exceptional, the continual advancement of technology guarantees even higher jumps ahead in the area of plastic extrusion equipment.Technologies in Extrusion Procedures
Harnessing the power of modern technology, plastic extrusion processes are undergoing a transformative metamorphosis. Developments content such as computerized numerical control (CNC) systems now permit more precision and consistency in the manufacturing of extruded plastic. Automation better boosts efficiency, reducing human mistake and labor prices. The assimilation of fabricated knowledge (AI) and artificial intelligence (ML) algorithms is changing top quality control, anticipating variances, and improving the overall efficiency of extrusion processes. With the advent of 3D printing, the plastic extrusion landscape is also increasing right into new worlds of opportunity. These technological advancements are not only boosting the top quality of extruded plastic products but additionally driving the market towards a more lasting, effective, and innovative future.Real-World Applications of Plastic Extrusion
Plastic extrusion, a efficient and versatile process, discovers usage in numerous real-world applications. The automotive industry also harnesses this modern technology to produce parts like trim and plastic sheet. The stamina and versatility of plastic extrusion, combined with its cost-effectiveness, make it a vital procedure throughout numerous sectors, underscoring its prevalent sensible applications.The Future of Plastic Extrusion: Forecasts and Patterns
As we look to the horizon, it comes to be clear that plastic extrusion is poised for substantial developments and makeover. Environmentally friendly choices to standard plastic, such as bioplastics, are additionally expected to obtain traction. These patterns show a dynamic, progressing future for plastic extrusion, driven by technological technology and a commitment to sustainability.
Conclusion
To conclude, plastic extrusion is an intricate process that makes use of advanced technology and varied products to develop varied items. Technological developments, click to read such as digital controls, boost the production process and guarantee constant results. The industry's focus on sustainability and intelligent equipment recommends an appealing future. As plastic manufacturing remains to evolve, it remains a vital part of lots of sectors worldwide.In essence, plastic extrusion is a high-volume production process in which raw plastic material is melted and created into a continual profile.While plastic extrusion is a commonly made use of strategy in production, the materials utilized in this procedure substantially affect its final output. At its core, plastic extrusion entails changing raw plastic material right into a continual profiled form. It has led home to the development of innovative extrusion equipment, which has boosted the performance and high quality of the plastic extrusion procedure.In final thought, plastic extrusion is a complicated procedure that makes use of sophisticated technology and varied products to create varied products.
Report this wiki page